Date of Award
12-16-2013
Document Type
Open Access Dissertation
Department
Nuclear Engineering
First Advisor
Travis W Knight
Abstract
Uranium hexafluoride (UF6) containment cylinders must be emptied and washed every five years in order to undergo recertification, according to ANSI standards. During the emptying of the UF6 from the cylinders, a thin residue, or heel, of UF6 is left behind. This heel must be removed in order for recertification to take place.
To remove it, the inside of the containment cylinder is washed with acid and the resulting solution generally contains three or four kilograms of uranium. Thus, before the liquid solution can be disposed of, the uranium must be separated. A modified sodium diuranate (SDU) uranium recovery process was studied to support development of a commercial process. This process was sought to ensure complete uranium recovery, at high purity, in order that it might be reused in the nuclear fuel cycle. An experimental procedure was designed and carried out in order to verify the effectiveness of the commercial process in a laboratory setting.
The experiments involved a small quantity of dried UO2F2 powder that was dosed with 3wt% FeF3 and was dissolved in water to simulate the cylinder wash solution. Each experiment series started with a measured amount of this powder mixture which was dissolved in enough water to make a solution containing about 120 gmU/liter.
The experiments involved validating the modified SDU extraction process. A potassium diuranate (KDU) process was also attempted. Very little information exists regarding such a process, so the task was undertaken to evaluate its efficacy and determine whether a potassium process yields any significant differences or advantages as compared to a sodium process. However, the KDU process ultimately proved ineffective and was abandoned. Each of the experiments was organized into a series of procedures that started with the UO2F2 powder being dissolved in water, and proceeded through the steps needed to first convert the uranium to a diuranate precipitate, then to a carbonate complex solution, and finally to a uranyl peroxide (UO4) precipitate product. Evaluation of operating technique, uranium recovery efficiency, and final product purity were part of each experiment. Evaluation of a technique for removing fluoride from the diuranate precipitation byproduct filtrate using granular calcite was also included at the end of the uranium recovery testing. It was observed that precipitation of sodium diuranate (SDU) was very nearly complete at a pH of 11-12, using room temperature conditions. Uranium residuals in the filtrate ranged from 3.6 - 19.6 ppm, meaning almost complete precipitation as SDU. It was postulated and then verified that a tailing reaction occurs in the SDU precipitation, which necessitates a digestion period of about 2 hours to complete the precipitation. Further, it was shown, during this phase of the process, that a partial precipitation step at pH 5.5 did not adequately separate iron contamination due to an overlap of uranium and iron precipitations at that condition.
Carbonate extraction of the SDU required an extended (3-4 hours) digestion at 40°C and pH 7-8 to complete, with sodium bicarbonate found to be the preferred extractant. The carbonate extraction was also proven to successfully separate the iron contamination from the uranium.
Potassium-based chemistry did produce a potassium diuranate (KDU) analogue of SDU, but the subsequent carbonate extraction using either potassium bicarbonate or potassium carbonate proved to be too difficult and was incomplete. The potassium testing was terminated at this step.
The uranyl peroxide precipitation was found to operate best at pH 3.5 - 4.0, at room temperature, and required an expected, extended digestion period of 8 -10 hours. The reaction was nearly complete at those conditions, with a filtrate residual ranging from 2.4 to 36.8 ppmU. The uranyl peroxide itself was very pure, with impurity averages at a very low 0.8 ppmNa and 0.004 ppmFe. ASTM maximum levels are 20 ppmNa and 150 ppmFe.
Fluoride removal from the SDU precipitation filtrate required multiple passes of the solution through a calcite bed with acid additions to adjust the pH back down to below 6 before each pass to allow the removal reaction to proceed. This result was a modification of the single pass technique that was planned due to the apparent shutdown of the NaF/calcite reaction at pH above about 10.
Conclusions drawn from the testing were that the results demonstrated a workable and effective series of processing steps. Techniques developed from the tests will make uranium recovery viable when transferred to the commercial process design.
Rights
© 2013, Austin Dean Meredith
Recommended Citation
Meredith, A. D.(2013). Modified Sodium Diuranate Process For the Recovery of Uranium From Uranium Hexafluoride Transport Cylinder Wash Solution. (Doctoral dissertation). Retrieved from https://scholarcommons.sc.edu/etd/2466
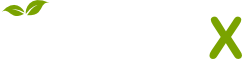
- Citations
- Patent Family Citations: 1
- Usage
- Downloads: 2804
- Abstract Views: 286
- Mentions
- References: 3